What is Porosity in Welding: Trick Aspects and Their Effect On Weld High Quality
What is Porosity in Welding: Trick Aspects and Their Effect On Weld High Quality
Blog Article
The Science Behind Porosity: A Comprehensive Guide for Welders and Fabricators
Understanding the detailed systems behind porosity in welding is essential for welders and fabricators striving for remarkable craftsmanship. As metalworkers explore the depths of this sensation, they discover a world controlled by various elements that affect the development of these minuscule gaps within welds. From the structure of the base materials to the intricacies of the welding procedure itself, a wide range of variables conspire to either intensify or minimize the visibility of porosity. In this extensive guide, we will certainly unravel the science behind porosity, exploring its impacts on weld top quality and introduction advanced methods for its control. Join us on this trip with the microcosm of welding blemishes, where accuracy satisfies understanding in the pursuit of flawless welds.
Understanding Porosity in Welding
FIRST SENTENCE:
Exam of porosity in welding exposes critical insights right into the honesty and high quality of the weld joint. Porosity, defined by the presence of cavities or spaces within the weld steel, is a typical concern in welding processes. These gaps, otherwise effectively dealt with, can compromise the architectural honesty and mechanical residential properties of the weld, causing potential failures in the finished product.
To spot and evaluate porosity, non-destructive screening methods such as ultrasonic screening or X-ray inspection are often employed. These methods enable the identification of interior issues without endangering the integrity of the weld. By examining the size, form, and distribution of porosity within a weld, welders can make educated decisions to enhance their welding procedures and accomplish sounder weld joints.

Factors Influencing Porosity Development
The incident of porosity in welding is influenced by a myriad of aspects, ranging from gas shielding efficiency to the details of welding specification settings. One important factor contributing to porosity development is insufficient gas protecting. When the shielding gas, commonly argon or carbon dioxide, is not effectively covering the weld swimming pool, atmospheric gases like oxygen and nitrogen can pollute the liquified steel, leading to porosity. Furthermore, the cleanliness of the base products plays a significant role. Pollutants such as rust, oil, or wetness can vaporize during welding, developing gas pockets within the weld. Welding parameters, consisting of voltage, existing, travel rate, and electrode kind, likewise influence porosity formation. Using improper setups can create excessive spatter or warm input, which consequently can lead to porosity. Additionally, the welding method used, such as gas steel arc welding (GMAW) or shielded metal arc welding (SMAW), can influence porosity formation due to variants in heat distribution and gas coverage. Comprehending and managing these aspects are crucial for decreasing porosity in welding procedures.
Results of Porosity on Weld Top Quality
Porosity formation dramatically jeopardizes the architectural honesty and mechanical homes of welded joints. When porosity exists in a weld, it produces voids or dental caries within the product, minimizing the total strength of the joint. These gaps function as anxiety focus factors, making the weld extra at risk to fracturing and failure under lots. The visibility of porosity also weakens the weld's resistance to corrosion, as the caught air or gases within the gaps can react with the surrounding atmosphere, bring about degradation over time. Additionally, porosity can prevent the weld's capacity to endure pressure or impact, my company more threatening the total top quality and dependability of the bonded structure. In vital applications such as aerospace, vehicle, or architectural building and constructions, where safety and longevity are vital, the detrimental results of porosity on weld top quality can have serious effects, emphasizing the importance of lessening porosity with appropriate welding strategies and procedures.
Methods to Lessen Porosity
Furthermore, utilizing the suitable welding specifications, such as the correct voltage, existing, special info and take a trip rate, is critical in preventing porosity. Maintaining a constant arc size and angle during welding additionally helps reduce the probability of porosity.

Moreover, picking the ideal shielding gas and preserving appropriate gas circulation prices look at these guys are essential in reducing porosity. Making use of the proper welding technique, such as back-stepping or utilizing a weaving motion, can likewise assist disperse heat equally and lower the opportunities of porosity formation. Finally, ensuring correct air flow in the welding atmosphere to get rid of any possible resources of contamination is essential for accomplishing porosity-free welds. By carrying out these strategies, welders can successfully decrease porosity and generate top quality bonded joints.
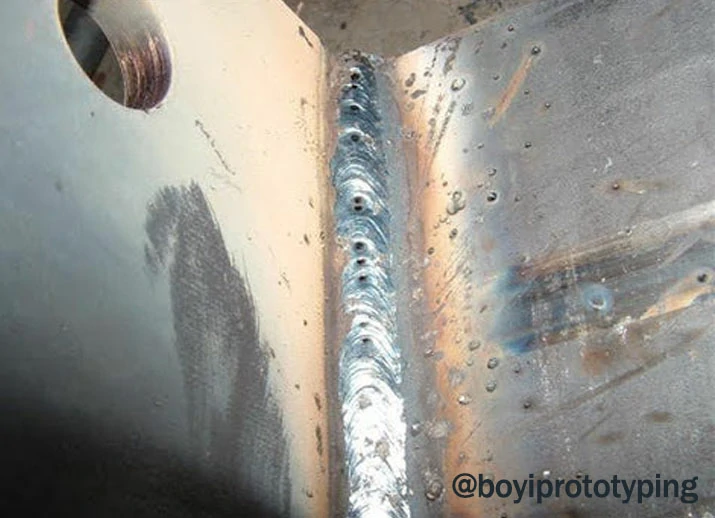
Advanced Solutions for Porosity Control
Executing cutting-edge modern technologies and innovative methods plays a pivotal function in attaining remarkable control over porosity in welding procedures. Furthermore, employing sophisticated welding strategies such as pulsed MIG welding or changed ambience welding can also assist reduce porosity concerns.
One more sophisticated option entails making use of innovative welding tools. Making use of tools with built-in attributes like waveform control and advanced power sources can boost weld high quality and reduce porosity dangers. The implementation of automated welding systems with precise control over parameters can considerably reduce porosity problems.
Moreover, integrating advanced monitoring and evaluation modern technologies such as real-time X-ray imaging or automated ultrasonic testing can aid in identifying porosity early in the welding procedure, enabling immediate corrective actions. Generally, integrating these innovative solutions can substantially improve porosity control and boost the overall top quality of bonded parts.
Final Thought
In final thought, understanding the science behind porosity in welding is crucial for welders and fabricators to create top notch welds - What is Porosity. Advanced remedies for porosity control can even more enhance the welding procedure and make certain a solid and trustworthy weld.
Report this page